K-Rock +
Metal packaging
Metal containers are very present in consumer goods, from cosmetics to food, to decorative and industrial containers and aerosols, among others. Its acceptance and extension to all spheres of daily life is given by its versatility and functionality, coupled with its strength, durability and circularity, since they are 100% recyclable. The metal industry is engaged in the manufacture of metal containers, mainly tin or aluminium.
Strong industry automation has drastically streamlined production processes. However, the greatest risk for the hands remains mainly suffering cuts when handling raw materials or parts.
The main raw materials are: tin, which consists of electrolytically coated steel; and aluminium. The working material is presented in rolls.
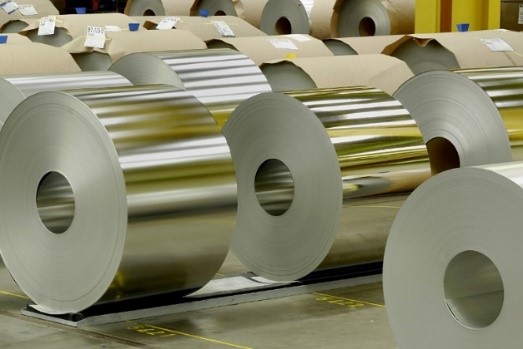
Receipt of raw materials and storage.

Material reception and storage operations involve mechanical risks when handling means of transport and lifting, as well as cutting, since the treated cargo is highly shear. Tin or aluminium rolls are stored before being cut at the beginning of the production phase.

Gloves by phases
Cutting phase

In the cutting phase, the metal rolls are placed in the primary cutting machines, which unwind and extract, according to the required shape, the small metal sheets that serve to shape the body, the bottom and the dome. At this stage, operators have direct contact with the highly shear metal sheet, having to place the rolls in the machines and having to take off the cut sheets. High protection against cuts with firm grip, mobility and dexterity is required.
The bottom and the dome are extracted from the secondary cut, where there is a high risk of cuts.

Gloves by phases
Lithography

Lithography is the packaging decoration phase in which coatings are applied to the sheets to give the packaging the image required by the customer.

Gloves by phases
Painting
After placing the sheets on the printing line, paints with the design of the final product are applied. Afterwards, varnishes are used to protect the paint. At this stage there are risks related to cuts and handling of chemical products.
Drying phase
In the final phase of lithography, the painted sheets are placed in the oven at 200º. The main issue here is thermal risk and risk of cuts, which is always present.
Printing

In the printing phase, the shape is given to the container by presses that cut and shape the sheets. The operator is in risk of cuts and abrasion.
Assembly

During the assembly phase, the container is completed by attaching all the parts. The dome may be mounted or removed, depending on the product to be contained in the container. The machines bend the sheets and apply the definitive shape by welding the elements that make up the container (crimped).
The risks of this phase are minor cuts, abrasion and heat from contact.
Packaging

The process in which the finished product is prepared for distribution. Materials such as cardboard, wood and plastic are handled in these operations. In addition, the gloves must facilitate the use of touch screens for recording the operations.
Logistics

In the logistics department, raw materials are received in the warehouse, components are delivered to the production lines and the final product is shipped via transportation companies.
The main hazards are cuts and abrasions. Protection against cold is occasionally required. Gloves must be prepared for touchscreen terminals.

Gloves by phases
Logistics
Guantes